Современная автомобильная шина является достаточно сложным с точки зрения технологического процесса продуктом. Несмотря на её привычный внешний вид и на первый взгляд простую конструкцию, у шины довольно сложное строения, а её производство – это сложный, многоэтапный капиталоёмкий процесс. Конструктивно автомобильная покрышка состоит из каркаса, бреккера, которого может быть несколько слоёв, протектора, бортовой части и боковины.
Основным материалами, из которых изготавливается автомобильная покрышка, является резина. Она состоит из каучуков и множества других компонентов. Ещё один важный элемент – корд, который может быть из металлических нитей – металлокорд, или из полимерных или текстильных волокон.
Маталлокорд применяется, как правило, для изготовления покрышек для грузового транспорта, а текстильный и полимерный – для легковых авто и лёгкого коммерческого транспорта. Брекер представляет собой достаточно толстый резиновый слой, расположенный между каркасом покрышки и протектором. Он демпфирует удары, защищая тем самым каркас. Протектор – это видимая часть автомобильной покрышки, которая служит для обеспечения сцепления с дорожным покрытием. Борт обеспечивает герметичность при монтаже покрышки на обод колеса. А боковая часть защищается покрышку от боковых ударов.
Этапы технологического процесса создания автомобильных шин
Каждая модель шины, прежде чем оказаться в продаже, проходит сложный процесс разработки и производства, который состоит из создания образца, его тестирования и непосредственного серийного производства, включающего подготовку резиновой смеси, производство компонентов автошины, сборку автошины, вулканизацию и контроль качества.
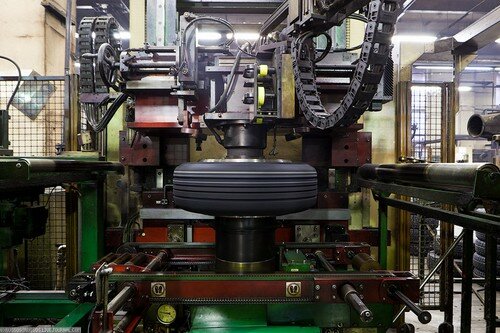
Разработки и тестирование образца
Всё начинается с процесса разработки. Он проходит с помощью специальных программных комплексов. В программе создаются разные модификации протекторов и профиля покрышек, которые, по мнению инженеров, должны удовлетворять задачам, стоящим перед разрабатываемой моделью. Затем эти компьютерные прототипы помещают в различные заранее смоделированные с помощью компьютерных программ ситуации и просчитывают, как каждая созданная виртуальная покрышка будет вести себя на дороге в той или иной обстановке.
Виртуальная шина, которая показала лучшие результаты, изготавливается ограниченным тиражом и проходит уже реальные дорожные испытания. Результаты тестов сравнивают с показателями шин аналогичного класса, при необходимости шине проводят процесс доводки, после чего её запускают в серийное производство.
На большинстве крупных заводов по изготовлению автомобильных шин производственные процессы практически полностью автоматизированы. В комплект оборудования входят формовочные машины, холодильные установки, протекторные линии, участки экструзии, резиносмесители, вулканизаторы и много другого оборудования.
Производство резиновой смеси
Первым этапом в серийном производстве покрышек является изготовление резиносмеси. Надо сказать, что у каждого производителя имеется свои рецептуры резиновых смесей, которые они хранят в строжайшем секрете. Однако основные ингредиенты и их примерные пропорции известны. Это такие материалы как:
– натуральный каучук, материал, который получают из сока гевеи бразильской – дерева специально выращиваемого на плантациях, в большинстве расположенных в Южной и Юго-Восточной Азии, а также в Западной Африке;
– синтетический каучук, который может быть изопреновым, бутадиеновым, бутадиен-метилстирольным, хлоропреновым, этиленпропиленовым;
– техуглерод или, как ещё называют этот компонент резиносмеси, «промышленная сажа», придающий резины характерный чёрный цвет, повышающий её прочность и стойкость к истиранию;
– кремниевая кислота – силика, которая является аналогом технического углерода и служит для повышения уровня сцепления покрышки на льду, укатанном снегу и на мокрой дороге;
– натуральные масла и смолы, выполняющие функции вспомогательных элементов для смягчения резины;
– сера и другие вулканизационные активаторы.
Все компоненты смешиваются до получения однородной массы. Процесс смешения происходит в герметичном смесителе при температуре 120°С. Следует понимать, что в разных частях применяются разные смеси, для которых подбираются необходимые материалы, устанавливаются свои пропорции компонентов, температура и скорость смешивания. Для протектора применяются резины одного типа, а для остальных элементов шины – другого. Достаточно сказать, что в одной автошине используется несколько марок технического углерода, которые отличаются параметрами.
Изготовление деталей автошины
На этом этапе происходит ряд параллельных процессов. Изготавливается прорезиненная лента, которая является заготовкой для протектора. Она нарезается на части по размерам, соответствующим размерам шины. Одновременно изготавливается шинный каркаса и брекер, которые предназначены для придания конструкции жёсткости и устойчивости к механическим повреждениям. На отдельных производственных участках изготавливаются борта и боковые. На этом этапе производится пропитка материалов, сушка, термическая обработка, прорезинивание бортовых колец, текстильного корда, стального брекера.
Сборка шин
Сборочные работы проводятся на специальной сборочном станке, на котором последовательно укладываются друг на друга слои для каркаса, бортовых частей и протектора с боковинами покрышки. Фактически такой станок представляет собой автоматизированный сборочный комплекс, который управляется оператором. Процесс сборки достаточно сложный. Он происходит на двух барабанах. На одном происходит сборка каркаса, а на другом – боковой части, после чего оба барабана совмещаются и сильно прижимаются до получения формы покрышки. На современном производстве участок сборки оснащён сразу несколькими такими сборочными комплексами. Для шин разного размера, больших, средних и малых.
Вулканизация
После окончания сборочных работ производится процедура вулканизации. Она проходит в специальном отверждающем прессе, который ещё называют «вулканизатором». В этой установке покрышка укладывается в форму, где под давлением воды и пара происходит формирование протектора. Процесс вулканизации происходит под действием высокой температуры и давлении, при которых каучук становится эластичным. В результате покрышка приобретает заданные структуру протектора и степень эластичности.
Контроль качества
Заключительным этапом является проверка качества готовой шины. У каждого производителя технология контроля качества своя, но в целом эта процедура сводится к визуальному осмотру и проверке качественных характеристик шины на специальном оборудовании – тестовых стендах. После комплекса проверок покрышка маркируется путём нанесения типоразмера, индекса скорости и нагрузки.
Так производятся современные шины. Причём как зимние, так и летние и всесезонные. Технологии производства автомобильных покрышек не стоят на месте. Процесс их развития совершенствуется постоянно, что доказывают постоянные инновации, которые можно видеть в новых моделях автошин, ежегодно представляемых известными шинными брендами.